El recubrimiento interior es uno de los tratamientos más habituales para luchar contra el pitting en los depósitos de ACS. ¿Conoces cuándo y cómo llevarlo a cabo?
En el post anterior dedicado a los procedimientos anti-pitting te hablamos sobre la posibilidad de realizar una soldadura de reparación de la zona afectada y generar un recubrimiento interior y comentamos que dedicaríamos un artículo especialmente a este tipo de recubrimientos internos para proteger el depósito.
Para ello redactamos este post. Para explicarte más a fondo cómo se realiza el recubrimiento interno en los depósitos de ACS.
Recubrimiento interno para la protección de depósitos de ACS
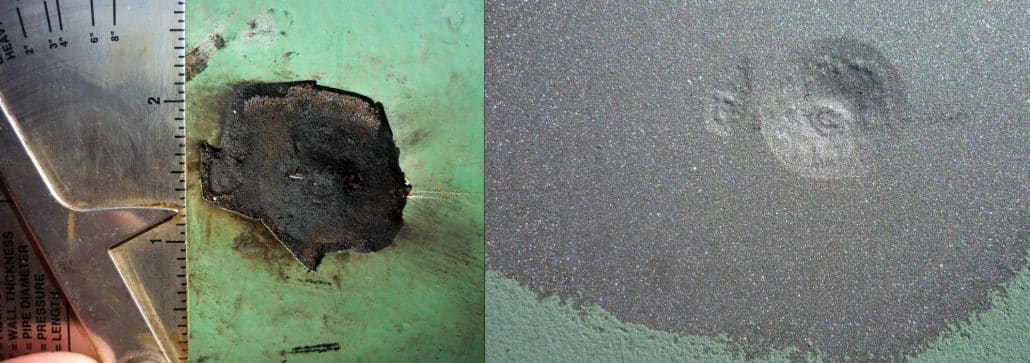
Cuando los acumuladores están afectados, pueden ser tratados interiormente para conseguir aislar el cuerpo de acero de los agentes agresivos del agua.
El proceso es simple y complicado a la vez. En primer lugar, tal y como avanzamos en las primeras frases del post, el primer paso es identificar y escoger el momento y tratamiento idóneos para la rehabilitación del depósito de ACS.
Existen muchos tipos de tratamiento y todos tienen sus pros y contras. Tanto el análisis como la reparación deben ser realizados por empresas especializadas del sector con reconocida solvencia. Hay que asegurar la garantía del trabajo realizado, puesto que son muchas las variables que pueden llevarnos a un fracaso en la reparación.
¿Cuándo se plantea el recubrimiento interno como solución al pitting?
Después de unos pocos años usando un nuevo depósito acumulador de Agua Caliente Sanitaria (ACS) empezarán a aparecer en el agua síntomas de corrosión (coloración rojiza), incluso cumpliendo estrictamente las recomendaciones de los fabricantes de equipos.
En los primeros estadios de este deterioro, cuando todavía se van salvando las revisiones sanitarias obligatorias gracias a las limpiezas e higienizaciones periódicas y las reparaciones son menores y de bajo coste, no se suele plantear su sustitución. En cambio, cuando estas medidas no son suficientes se empieza a estudiar la posibilidad de sustituirlo o al menos rehabilitar.
En la mayoría de casos es inviable la sustitución del depósito por otro igual por el desmontaje y gestión de residuos que genere el viejo depósito junto al coste del nuevo además de rotura de paredes y techos y uso de maquinaria pesada para su colocación.
Para seguir usando el viejo depósito se suele recurrir al recubrimiento interno. A continuación explicamos las fases para este procedimiento de reparación de depósitos de acumulación de ACS.
¿Te gusta lo que estás leyendo?
¡Suscríbete a nuestra newsletter!
Fases del recubrimiento interno de un depósito de ACS
1ª Fase: Inspección de sus paredes (soporte)
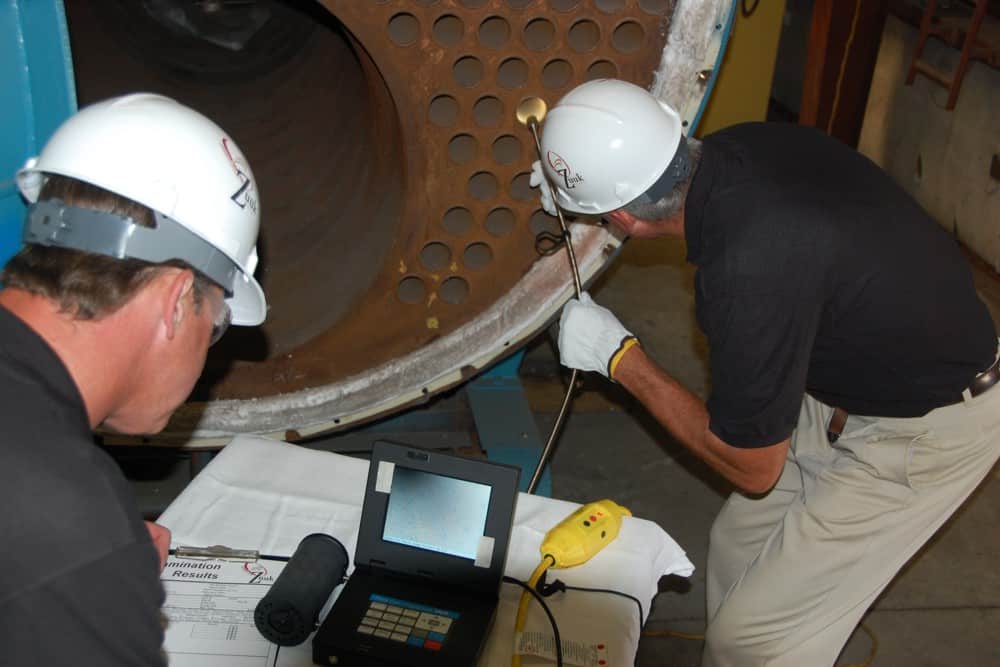
Esta parte es muy importante, puesto que debe marcar los procedimientos adecuados a seguir en el resto de fases.
“Fallar en la preparación es prepararse para fallar”
La búsqueda de posibles corrosiones y poros puede ser desde una simple ojeada a toda la superficie interna del depósito hasta la utilización de métodos no invasivos, a cada cual más preciso:
- Líquidos penetrantes: Por capilaridad señalan discontinuidades y oquedades en la superficie metálica interna.
- Partículas magnéticas: Al aplicar polvo de hierro en la superficie interna con un campo magnético en la contraria, se detectan imperfecciones en el metal al moverlo por su superficie.
- Radiografía: Usando Rayos X o Rayos Gamma que atraviesan el metal resulta en una impresión fotográfica que revela el estado de su estructura interna.
- Ultrasonidos: Una onda de sonido de alta frecuencia al atravesar el metal “dibuja” en una pantalla el estado tanto de su estructura interna como de la superficial.
2ª Fase: Granallado interno
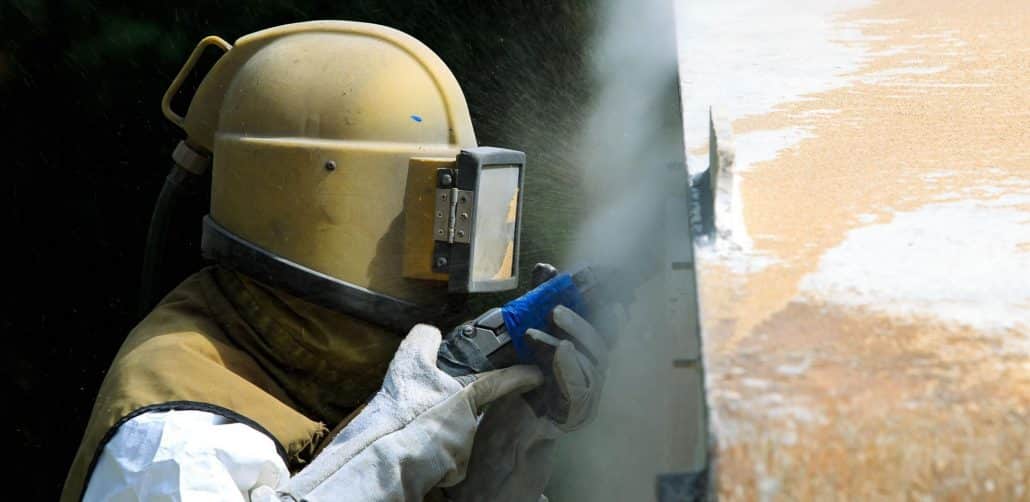
Para la adecuada adhesión del recubrimiento, el soporte debe estar lo más límpio y poroso posible, se debe minimizar la presencia de óxidos, pinturas, suciedades y grasas y los daños por óxido (gracias a la detección en el paso anterior).
Tratar la superficie del metal mediante granallado con el método del “chorreado abrasivo” como un mínimo recomendable, siempre es preferible a la “limpieza manual”.
Dicho método se puede hacer en diferentes grados de calidad (norma ISO 8501-1):
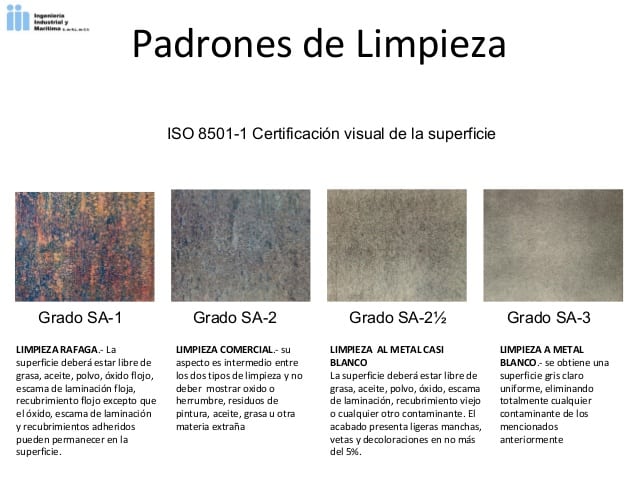
- Desde un “chorreado ligero” (SA-1): elimina capas sueltas de laminación, óxido y partículas extrañas…
- … hasta el más exhaustivo “chorreado a metal blanco” (SA-3): elimina la totalidad de óxido visible y de otros restos…
- … siendo el más habitual el “chorreado muy minucioso” (SA-2½ ): queda al 95% libre de cualquier residuo visible…
- … aunque a veces se quedan en el “chorreado minucioso” (SA-2): limpio al 66%.
Tras el chorreado se retiran los restos de polvo abrasivo y los desprendidos con aire comprimido seco y aspirador.
El proceso de secado es importantísimo para evitar que la presencia de micro-gotas de agua permanezcan en los poros del acumulador. Si el proceso de secado no es completo, la probabilidad de que el recubrimiento falle es altísimo. Estos procesos son muy importantes para asegurar que las aplicaciones posteriores sean efectivas y duraderas.
3ª Fase: Protección de soldaduras internas
A los cordones de soldadura interna se les debe conceder especial atención ya que son las zonas más sensibles y difíciles de tratar por su natural rugosidad y variabilidad de composición.
En la primera fase se debieron revisar y mejoraba el estado estructural de las soldaduras. Pero para taponar en la medida de lo posible las erosiones o poros que aún pueda presentar las soldaduras se les suele pre-recubrir con electro-galvanización (EG): Se fijan capas de zinc a la soldadura mediante un procedimiento electrolítico. (Este proceso no suele utilizarse por su alto coste y posibles problemas de adherencia con algunos de los revestimientos que se aplicarán con posterioridad)
Para terminar esta fase se retira escrupulosamente cualquier resto, se higieniza con productos que no dejen residuos y se usa secador en toda la superficie interna a conciencia, tratando de alcanzar temperaturas que faciliten la mayor evaporación posible del agua retenida en las micro-fisuras.
En estos momentos, como el metal está más expuesto que nunca a agentes oxidantes, la siguiente fase debe ser inmediata.
4ª Fase: Aplicación interna del recubrimiento
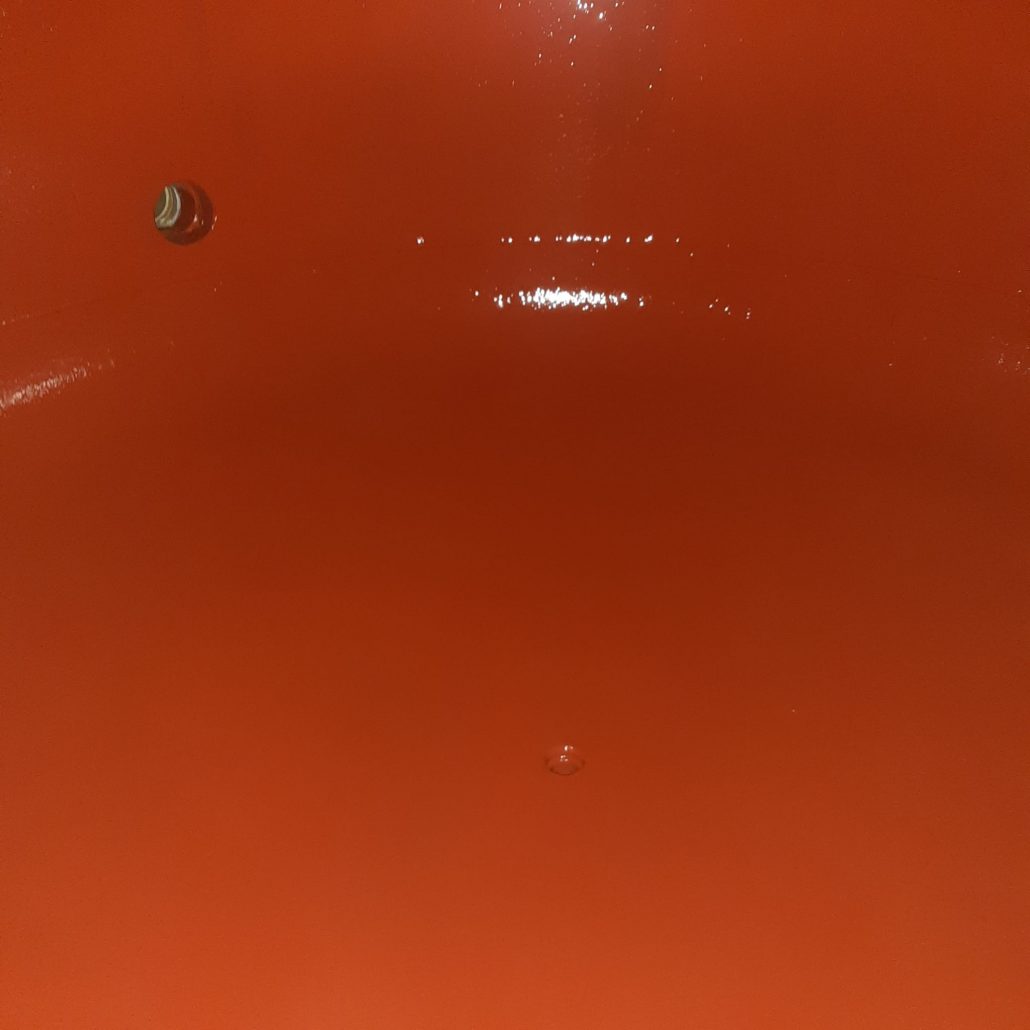
Estos recubrimientos, además de no transmitir al agua componentes que la invaliden para consumo humano (R.D. 140/2003), deben presentar alta durabilidad tanto ante los choques térmicos del agua que contendrán como ante los productos y tratamientos de higienización que periódicamente se realizarán para cumplir con la normativa de mantenimiento.
La aplicación del recubrimiento requiere de una primera capa de imprimación que actúa de catalizador del producto base, activando así todas sus propiedades. Cada tipo de recubrimiento requiere su propia imprimación.
Del producto base se suelen aplicar de dos a cuatro capas, normalmente de entre 100 y 200 micras cada una. Es muy importante respetar los tiempos de curado entre capas atendiendo a las recomendaciones del fabricante y las temperaturas a las que se aplica el producto.
Es muy común el error de querer dar la siguiente capa antes de lo recomendado por el cliente. Los perjuicios que generamos al no haber permitido que se complete la reticulación química de la capa previa, seguro superan al beneficio de acabar un poco antes. (Imprescindible contratar empresas de reconocida solvencia que prioricen la garantía de su trabajo por encima del beneficio económico.)
Existen diferentes calidades en los tipos de recubrimiento. El usado más habitualmente es la resina epoxi por su económica relación precio-fiabilidad pero que ofrece sólo hasta 3 años de durabilidad en el mejor de los casos. Otro compuesto, la resina polimérica o poliurea, es más costosa pero con tiempos de curado mucho menores y más flexible a iguales choques térmicos que la epoxi con lo que se le puede otorgar hasta unos 5 años de vida útil.
Los acabados internos y el cuidado en la aplicación son fundamentales. Los buenos resultados dependen de que cuando llenemos el acumulador, el agua no consiga penetrar entre el recubrimiento y el acero por ningún hueco o resquicio. En caso que esto suceda, habremos echado a perder todo el trabajo de recubrimiento.
¿Si recubrimos el acumulador, durará indefinidamente?
En la teoría si, pero lamentamos comunicarte que no es cierto. Podríamos decir que el revestimiento es casi indefinido si:
a) El soporte estuviese en perfectas condiciones.
b) Las soldaduras fuesen perfectas.
c) El producto a utilizar sea el adecuado.
d) El revestimiento mantuviese sus características físico-químicas de forma indefinida.
e) Tuviésemos la certeza de que el agua que contendrá el acumulador no podrá entrar de ningún modo entre el revestimiento interior y el acero.
Como es prácticamente imposible que la totalidad de los condicionantes se cumplan al 100%, podemos asegurar que tarde o temprano el revestimiento aplicado o su adherencia soporte fallará.
Puede considerarse un buen método para alargar la vida de un acumulador durante unos meses o incluso algún año, pero no conocemos acumuladores revestidos que sean de uso intensivo y hayan durado más de 2 años.
¿Dónde suelen fallar este tipo de recubrimientos?
Suelen fallar en cualquiera de los puntos descritos en el apartado anterior.
Principalmente en el granallado y secado. Incluso en un recién aplicado recubrimiento interno queda retenida agua en las micro-fisuras que provoca la corrosión por pitting.
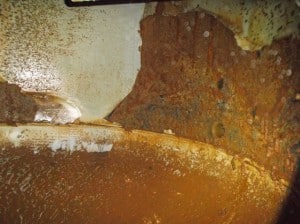
Por la propia química de este tipo de corrosión, progresará por un lado continuando su penetración en la pared metálica y por el otro hacia el revestimiento terminando por dañarlo.
En este momento te será fácil imaginar qué le puede suceder al depósito y al ACS que contiene cuando de nuevo se manifiesten las consecuencias de seguir afectado de pitting. De ello hablaremos en el próximo artículo.
¿Quieres saber más sobre las corrosiones producidas en las instalaciones de ACS?
FAQs sobre recubrimiento interno
¿Qué es el recubrimiento interno en el contexto de los depósitos de ACS?
El recubrimiento interno es un proceso utilizado en los depósitos de Agua Caliente Sanitaria (ACS) para proteger el interior del depósito de la corrosión y el pitting, aislando el cuerpo de acero del contacto con el agua corrosiva.
¿Cuándo es necesario considerar el recubrimiento interno como una solución para un depósito de ACS?
El recubrimiento interno se considera cuando el depósito de ACS muestra signos de corrosión, como coloración rojiza, incluso cuando se siguen las recomendaciones del fabricante y se realizan limpiezas periódicas.
¿Cuáles son los pasos clave en el proceso de recubrimiento interno de un depósito de ACS?
El proceso consta de varias fases: inspección de las paredes, granallado interno, protección de soldaduras internas y aplicación del recubrimiento.
¿Qué importancia tiene la inspección de las paredes del depósito en el proceso de recubrimiento interno?
La inspección es crucial para determinar el estado del depósito y planificar las siguientes fases del proceso. Se utilizan métodos como líquidos penetrantes, partículas magnéticas, radiografías y ultrasonidos.
¿Qué es el granallado interno y por qué es necesario?
El granallado interno es un proceso de limpieza que elimina óxidos, pinturas y suciedades de la superficie del depósito. Es esencial para garantizar una buena adhesión del recubrimiento.
¿Qué se hace para proteger las soldaduras internas durante el recubrimiento interno?
Las soldaduras internas, que son zonas sensibles, se suelen pre-recubrir con electro-galvanización para tapar erosiones o poros. Esto mejora su resistencia a la corrosión.
¿Qué tipos de recubrimientos se utilizan en el recubrimiento interno de depósitos de ACS?
Los recubrimientos más comunes son las resinas epoxi y las resinas poliméricas o poliurea. Cada tipo tiene sus propias características y durabilidad.
¿Qué cuidados se deben tener en cuenta durante la aplicación del recubrimiento interno?
Es fundamental seguir los tiempos de curado recomendados por el fabricante y respetar las temperaturas de aplicación. También es esencial evitar que el agua penetre entre el recubrimiento y el acero.
¿Cuánto tiempo puede durar un recubrimiento interno en un depósito de ACS?
La duración del recubrimiento depende de varios factores, incluyendo el estado del soporte, las soldaduras, el producto utilizado y la adherencia del recubrimiento. En la práctica, suele durar de unos meses a algunos años.
¿Dónde suelen fallar los recubrimientos internos en depósitos de ACS?
Los recubrimientos internos pueden fallar en varios puntos, especialmente en el granallado y el secado insuficiente, lo que permite que el proceso de corrosión continúe debajo del recubrimiento.